Sysmac Automation Platform
Sysmac is the latest machine automation platform from Omron with integration throughout: from controller to software.
The guiding principles behind the Sysmac automation platform are:
- One control for the entire machine or production cell
- Harmony between machine and people
- Open communication and open programming standards.
Since 1971 Sysmac has been used on PLCs, and has conveyed the Omron principles of reliability, robustness and fast control. Today we expand these principles across the whole machine.
Fastest Machine Network: To achieve the accuracy and predictability required by today’s machines, Omron selected EtherCAT, the fastest machine network. This is not only for motion, but IO, Safety and Vision. This gives a huge benefit to the customer simplifying the cabling and delivering astonishing performance.
Intel Architecture: Traditional ASIC based PLCs take time to develop and are not easy to change quickly. Sysmac uses an Intel® Atom™ or Core™ i7 processor and Real Time Operating System (RTOS) to shorten the development time and accelerate the ability to respond to new requirements. Performance can easily be scaled to suit the machine, without changing the design.
Integrating motion, sequencing, vision and networks in ONE machine controller gives you complete control over the entire machine with high performance and easy operation.
Key Controller Features
- EtherNet/IP and EtherCAT ports embedded
- Standard IEC 61131-3 programming
- Certified PLCopen Function Blocks for Motion Control
- Global standards CE, cULus, NK, LR
Machine Control Features
- Seamless integration of Logic and Motion
- Synchronous control of all machine network devices
- Backwards compatibility with most CJ PLC-series modules
Motion Control Features
- Control up to 256 axes of motion
- Linear and circular interpolation
- Electronic cam and gearing
EtherCAT is the fastest emerging network for machine automation. It’s fast, accurate and highly efficient for the total machine.
Key EtherCAT features
- Industrial Ethernet using standard IEEE 802.3 frames
- High synchronization accuracy by using a distributed clock mechanism
- The fastest network on the market with 100 μs refresh time and less than 1 μs jitter
- Simple to set up with automatic address assignment for nodes
- Uses standard Ethernet cables and connectors
- Flexible Network Topology
- On-the-Fly data exchange with slave devices for high throughput
- Supports up to 512 slaves
- Control Omron Servos, Inverters, Vision Systems, Robots, Distributed I/O, Safety, Sensors and more
One connection via the machine controller allows seamless control and communication with both the machine and the factory.
The Sysmac machine controllers join the world standard factory automation network, EtherNet/IP, with the best Ethernet-based machine control network, EtherCAT.
Key Ethernet/IP Features
- Peer-to-Peer controller communication
- Interface with NA HMI series or SCADA software
- Database connection for MS SQL Server, Oracle, MySQL, IBM DB2 and Firebird
- FTP
- Support MATLAB/Simulink simulation software
One software to control and configure the entire machine via a single connection gives you the power and efficiency to develop and create like never before.
Learn it once
- One software for logic, motion, safety, drives, vision and HMI
- Fully compliant with the open standard IEC 61131-3
- One consistent design environment
- Supports Ladder, Structured Text and Function Block programming with a comprehensive instruction set
- Graphical CAM editor for easy development and programming of complex motion profiles
- Intuitive editor with auto-complete assistance for Ladder and Structured Text programming
Test it as one
- One simulation tool for sequence and motion in a 3D environment
- Complete or partial program can be simulated and debugged
- Data trending for tuning and debugging
- Emulation of all Sysmac controllers functions
Secure it all
- Advanced security function with 32 digit security password
- Complete project or single Function Block can be protected (available in Sysmac Studio above v1.)
- Machine cloning prevention
- One Intuitive Interface
Applications

Vibration Suppression
Handling liquids at high speeds? Need to suppress vibration in motion applications? See how the Sysmac NJ Machine Automation Controller manages.
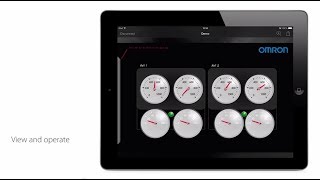
-
Introducing the Sysmac Remote Viewer for HMI
This video gives a brief introduction to the Sysmac Remote Viewer from Omron. The Remote Viewer is an app that allow remote connection to Omron HMI (NA, NS & NB).
02:42
Remote Viewer for Human Machine Interfaces
This video gives a brief introduction to HMI Remote Viewer.
What our customers think

Shop floor to top floor
International print system manufacturer Ricoh is set to create links between its UK toner cartridge production and refill operations and a factory-level database, using Omron control technology to allow two-way real-time communications for the first time.

-
HNC's Rubber Roll Grinders and Groovers featuring Omron Technology.
Introducing HNC's range of advanced Rubber Roll Grinders and Groovers. This range of innovative machines are used to precision grind the profiles of Rubber or Polyurethane rolls. The software built into HNC's range of Advanced Automatic Roll Grinders and Groovers greatly reduces the need for highly skilled operators. With a minimum of knowledge you can successfully profile rubber or polyurethane rollers up to 600 mm in diameter & many metres in length. The machine's software has both imperial (inch) & metric capability, and can be switched between sixteen different languages at the touch of a button. Each machine is fully automatic and comes complete with a fully enclosed interlocked guarding system and complete dust extraction tube ready to connect to a dust extractor. A Joint video production between Omron and Halifax Numerical Controls Ltd detailing the use of the NJ PLC on the RG300 Rubber roll grinder. The video highlights the use of the NJ controller on the RG300 rubber roll grinding machine.
05:08
Roll grinding made easy
"Sysmac controller provided a flexible platform" - Mike Diskin, Managing Director of Halifax Numerical Controls, UK