Ayabe Factory
Unlocking the full potential of on-site workers through curated automation and skill-less operation
OMRON Ayabe Factory is the site of ultra-high-mix low-volume production, where we manufacture approximately 20,000 items, ranging from sensors a few centimeters in size to inspection devices that are several meters large. It is mainly an assembly factory where high-quality products are efficiently produced by finely coordinating product design and process design activities. Processes within the production line that do not generate added value, such as transport, are automated to lessen the burden of on-site workers. Data obtained from the production floor is analyzed to visualize improvement points by uncovering procedural factors that affect production efficiency and quality. Tasks that traditionally required the skill and knowledge of veteran workers have been transformed into skill-free operations through automation.
Automating parts transport with mobile robots to allow human workers to focus on product value improvement
Enabling optimally timed maintenance through predictive management of optical element alignment device
Detecting the slightest shifts in robot hand position to reduce facility downtime and part loss
Enabling low-cost automation of inter-process material handling with compact autonomous transport robots
Robotizing complex soldering into skill-free operation without compromising precision or speed
Ayabe Factory
Ayabe
Kyoto 623-0105
Japan
Our Worldwide Production Facilities
Strategically implementing i-Automation! to create the factory of the future
read more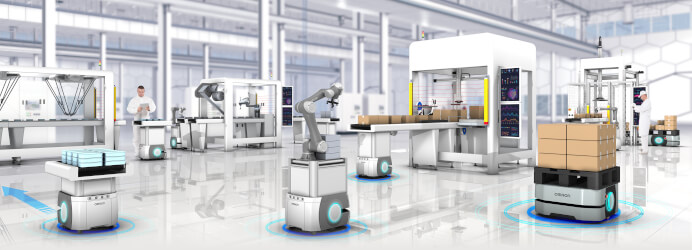