Cobot boosts production by 15% at Topcustom
Published on 23 June 2021 in Flexible Manufacturing
- 0:00 - Cobot boosts production by 15% at Topcustom

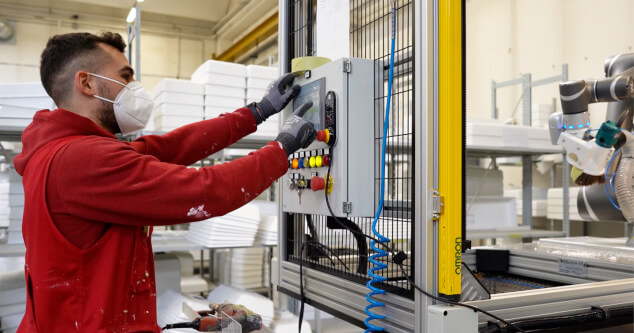
We are experiencing technical difficulties. Your form submission has not been successful. Please accept our apologies and try again later. Details: [details]
DownloadWe are experiencing technical difficulties. Your form submission has not been successful. Please accept our apologies and try again later. Details: [details]
DownloadFill in your details below and get direct access to view content
We are experiencing technical difficulties. Your form submission has not been successful. Please accept our apologies and try again later. Details: [details]
DownloadYou now have access to Cobot boosts production by 15% at Topcustom
A confirmation email has been sent to
Continue to pagePlease log in or get direct access to download this document
Published on 23 June 2021 in Flexible Manufacturing