Cobot ensures precise assembly of magnets for LITMAT’s drain plugs
Published on 03 June 2021 in Flexible Manufacturing
- 0:00 - Precise and consistent assembly of magnets and coatings with a cobot for the automotive market

Precision assembly with cobots
LITMAT recently decided to simplify the process of assembling the magnets that are needed to attract and remove any impurities in oil. The company therefore started looking for automated solutions, which led to the choice of OMRON’s TM5 cobot. This cobot is designed to be safe, simple to programme, and easy to integrate with other equipment. It represents a big step towards creating an intelligent manufacturing environment where people and machines work in harmony.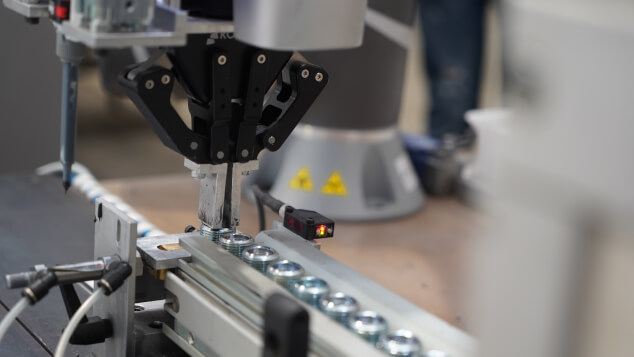