Shanghai Factory, China
Production site of approximately 23,000 different products that cater to changes in the Chinese market, powered by intensive digitalization and autonomation.
Our Shanghai Factory is a development/production site undergirding our factory automation (FA) business in China. It enables ultra-high-mix low-volume production of as many as approximately 23,000 different products, including PLCs, sensors, temperature controllers, power supplies, servo drivers, and robots. The factory takes on difficult challenges in manufacturing to promptly and stably supply the vast range of FA products demanded by the Chinese market, in turn securing our standing as a reliable manufacturer of control devices.
Our Shanghai Factory practices and demonstrates OMRON’s value-added manufacturing, even amid continuing changes in supply chain conditions. With quality as the top priority, it continues to improve productivity and quality by collecting and analyzing data from digitalized production lines. By combining Low Cost Intelligent Automation (LCIA) equipment, which enables low-cost autonomation by focusing on select points, with full automation equipment, the site allows for optimized human-machine collaboration to enable a production line that can advance both productivity and quality.
Improving productivity and quality in cellular manufacturing through human-machine collaboration
Detecting and addressing quality risks by constantly monitoring line and supply chain.
Production line management with CLCS allows us to track 4M (machines, manpower, methods, and material) conditions of parts suppliers and per-lot data on the results of inspections conducted in the course of manufacturing obtained through IoT technologies. This information is used to visualize risk factors that can undermine quality or productivity. We also use our production system’s Statistical Process Control (SPC) feature to detect signs of quality deterioration within the production process, so we can find and proactively take action against quality risks.
We additionally collect all relevant (4M) data from the production line to enable optimal quality inspections and use AI systems that incorporate quality improvement know-how to empower on-site workers to take proper and quick action for better quality.
Cutting lead time in cellular manufacturing by 2 hours through automated transport
Boosting productivity through human-machine collaboration enabling shorter depreciation of 1-2 years
Enabling stable and high-precision assessment through the autonomation of sensory inspections previously reliant on human eyesight
Ensuring safe and secure production through advanced human-machine collaboration
High-mix low-volume production tends to be incongruous with continuous production, due to its smaller per-order production volume and thus shorter production time with autonomated equipment. For this reason, applying autonomation methods designed for conventional continuous production in such scenarios offers poor return on investment.
Our Shanghai Factory is equipped with versatile collaborative robots that can work together with human workers and can be relocated and shared as needed between multiple equipments. This allows us to maintain high productivity levels even when line configurations are changed to accommodate different product items. The image systems of these robots are used to automate their positioning and correction upon relocation, and thereby configure operations suited for equipment conditions in their new process without the help of human eyesight. What’s more, this configuration can be easily completed with the press of a button
Shanghai Factory
Our Worldwide Production Facilities
Strategically implementing i-Automation! to create the factory of the future
read more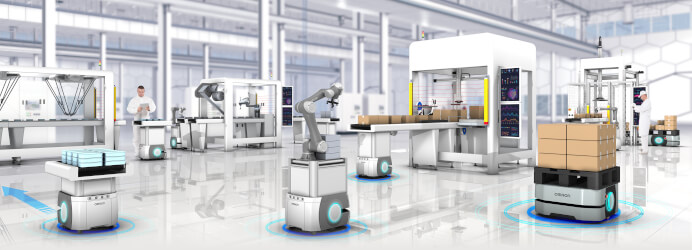